High-end bicycle disc brake pads represent the highest mechanical technology and material science level. There are various bicycle disc brake pads types in the market currently. The main difference among different bicycle disc brake pads lies in the different friction materials they use.

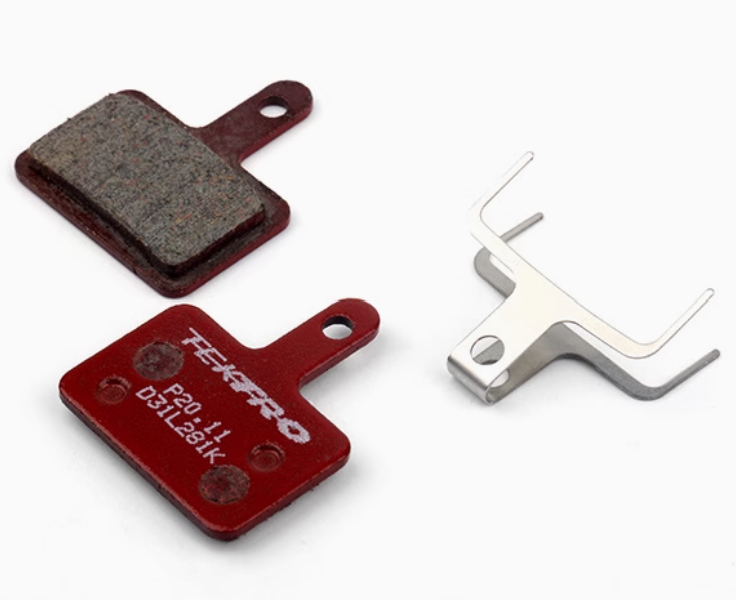
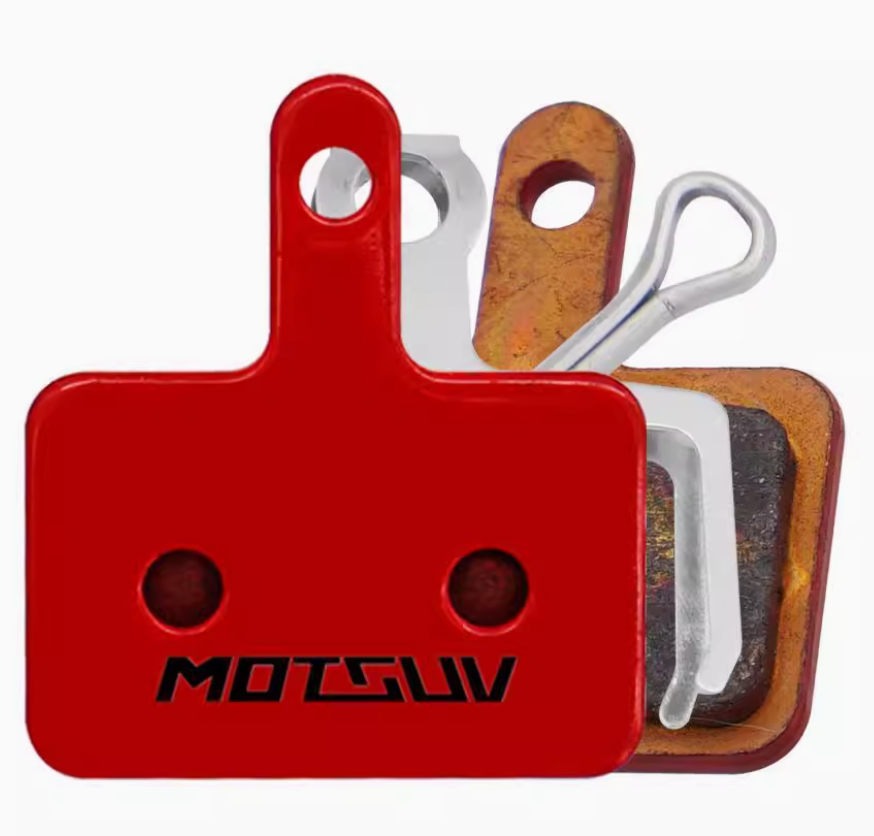
1. How is the friction material made in the factory?
Generally, manufacturers select different material powders. They mix these powders in a specific proportion. Finally, they produce the friction material through heat treatment. The manufacturing process of friction materials for bicycle disc brakes usually consists of the following steps:
1.1 Raw material preparation and mixing
Materials used may include reinforcing fibers (such as aramid, glass, carbon, or steel fibers), friction performance modifiers (like graphite and molybdenum disulfide), binders (such as phenolic resin and rubber), fillers (such as alumina and calcium carbonate), and other additives (such as anti – wear agents and antioxidants). These raw materials need to be accurately calculated and weighed according to different performance requirements. Then, put the prepared raw materials into a mixer in the set proportion and mix them thoroughly. During the mixing process, ensure that all materials are evenly distributed. This can guarantee the consistency of the friction material’s performance. Usually, a high – speed mixer is used. The mixing time depends on the types and quantities of materials, generally ranging from several hours to dozens of hours.
1.2 Hot pressing molding.
Put the mixed materials into a mold. Then, send them to a hot press for hot press molding. During the hot press process, precisely control parameters like temperature, pressure, and time. Generally, the temperature is around 150 – 200
°
C. The pressure ranges from dozens of megapascals to over a hundred megapascals. The holding time is from a few minutes to dozens of minutes. Under high – temperature and high – pressure conditions, the binder undergoes a curing reaction. This makes all materials combine tightly and form a friction material blank with a certain shape and size.
1.3 Heat treatment
The friction material blank after hot press molding usually needs heat treatment. Put the blank into a heat treatment furnace. Keep it at a certain temperature for a while to further improve the material’s performance. The heat treatment temperature is generally between 100 – 300°C. The treatment time may last several hours or even longer. Through heat treatment, the binder can be further cured and cross – linked. This enhances the material’s strength and stability. At the same time, it also improves the high – temperature resistance and friction performance of the friction material.
1.4 Grinding processing
The surface of the friction material after heat treatment may be uneven or have dimensional deviations. So, grinding processing is required. Use grinding equipment like surface grinders and cylindrical grinders. Finely grind the surface of the friction material to meet the specified dimensional accuracy and surface flatness requirements. During the grinding process, control the grinding speed, feed rate, and grinding time. This can avoid excessive wear or damage to the friction material.
2. Performance indicators of the friction material
The performance indicators of friction materials mainly include friction coefficient (braking effect), stability, service life, performance retention, high – temperature stability, thermal deformation and thermal fade, and mechanical strength.
2.1 Coefficient of friction (braking effect)
An appropriate friction coefficient is crucial for ensuring braking performance. If the friction coefficient is too high, the wheels may lock up instantly during braking. This will affect riding safety and controllability. If the friction coefficient is too low, the braking distance will be too long, and the vehicle cannot stop in time. For example, when a mountain bike is going downhill fast, reliable braking performance is needed to control the speed. This requires the friction coefficient of the brake pads to remain stable under different road conditions and speeds. Only in this way can precise braking control be achieved.
2.2 Stability
The friction coefficient of the friction material should remain relatively stable under different working conditions. When factors like temperature, humidity, and wear degree change, the fluctuation range of the friction coefficient should be small. For example, when riding in a humid environment, the friction coefficient of the friction material should not drop significantly due to the influence of moisture. This can ensure that the braking performance is not affected significantly.
2.3 Service life
Bicycle brake pads are frequently subject to braking friction. So, wear resistance is directly related to their service life. A friction material with good wear resistance can reduce the frequency of brake pad replacement. This can lower the use cost. For example, for bicycle enthusiasts who ride frequently, a pair of wear – resistant brake pads can be used for a long time without frequent replacement. This not only saves money but also improves the convenience of riding.
2.4 Performance retention
As the friction material wears, its performance should remain relatively stable. If it wears too quickly, it will not only make the brake pads thinner. It may also change the friction coefficient and affect the consistency of the braking effect. For example, during a long – distance ride, the wear of the brake pads should not cause the braking performance to gradually decline. Instead, it should always maintain reliable braking ability.
2.5 High – temperature stability
During frequent or high – intensity braking, the friction material generates a large amount of heat, causing the temperature to rise. Good heat resistance can ensure that the friction material still maintains stable performance at high temperatures. It can avoid the phenomenon of braking fade due to overheating. For example, during continuous long – distance braking when going downhill, the brake pads need to withstand the test of high temperatures. They should ensure that the braking performance does not decline and guarantee riding safety.
2.6 Thermal deformation and thermal fade.
Friction materials with poor heat resistance may deform, melt, or thermally decompose at high temperatures. Thus, they will lose their braking ability. At the same time, the phenomenon of thermal fade may occur. That is, as the temperature rises, the friction coefficient drops significantly. For example, in intense mountain biking or high – speed braking scenarios of road racing, the heat resistance of the brake pads is crucial. Otherwise, effective braking may not be possible due to thermal fade.
2.7 Mechanical strength
Brake pads are subjected to impact forces and pressures during braking. They need to have sufficient mechanical strength to withstand these forces. This can prevent damage such as cracking and peeling. For example, during emergency braking or when encountering a bumpy road, the brake pads should be able to withstand the instantaneous impact force. They should maintain their structural integrity to ensure that the braking performance is not affected.
3. Proportioning of raw materials determine the performance
Under similar processing techniques, among all bicycle disc brake pads types, the above – mentioned performance indicators are all determined by the materials selected for the friction material and the proportioning of these materials.
3.1 Coefficient of friction (braking effect)
Select materials with a high friction coefficient, such as aramid fibers and ceramic particles. This can directly increase the initial friction coefficient of the brake pads. It enables the generation of a greater frictional force during braking, achieving quick deceleration or stopping. Materials with self – lubricating properties like graphite, if added in excessive amounts, will reduce the friction coefficient and deteriorate the braking effect. However, an appropriate amount of addition can improve the friction performance. It can prevent the friction coefficient from being too high, which may make the braking too sensitive and difficult to control.
Increasing the proportion of materials with a high friction coefficient usually raises the overall friction coefficient and enhances the braking effect. But if the proportion is too high, it may cause the braking to be too sudden. The wheels are likely to lock up, affecting riding safety and controllability. Reasonably adjust the proportion of different materials. This can make the friction coefficient reach the ideal range. It can ensure both braking effect and riding comfort and controllability. For example, in a resin matrix, appropriately increase the content of short – fiber materials with good friction performance. This can effectively enhance the braking effect without making the braking too sensitive.
3.2 stability
Choose raw materials with stable performance, such as high – quality synthetic resin as the matrix material. This can provide a stable structural support for the friction material. It can reduce performance fluctuations caused by environmental factors (such as temperature and humidity changes). Some additives with special properties, such as antioxidants and anti – moisture agents, can improve the stability of the friction material under different environmental conditions. They can prevent the material from changing its performance due to oxidation, moisture, etc.
Optimize the proportioning of raw materials. Make each component interact synergistically. This can improve the stability of the friction coefficient. For example, adjust the ratio of fibers to resin. Make the fibers evenly distributed in the resin matrix. This can ensure that the friction coefficient remains relatively stable under different braking frequencies and intensities. Reasonably control the dosage of additives. This can not only play their role in improving stability but also avoid affecting other performances due to excessive addition. For example, an appropriate amount of anti – moisture agent can effectively reduce the impact of humidity on the friction coefficient. But excessive use may reduce the mechanical strength of the material.
3.3 service life
Wear – resistant raw materials, such as hard particles like silicon carbide and titanium boride, can improve the wear – resistance of the friction material. They can extend its service life. These hard particles can form a hard surface during the friction process to resist wear. Fibrous materials with good toughness, such as glass fibers and carbon fibers, can enhance the overall structural strength of the friction material. They can prevent cracks and peeling during use, thus extending the service life.
Increasing the proportion of wear – resistant materials can improve the wear – resistance of the friction material. However, if the proportion is too high, the material may become too hard. This will result in poor adhesion to the brake disc and instead affect the service life. For example, if the content of silicon carbide particles in the friction material is too high, it may scratch the brake disc. It will also increase the wear of the brake pads themselves. Reasonably adjust the proportion of fibers to the matrix material. This can make the friction material have good wear – resistance while maintaining appropriate flexibility and toughness. For example, optimize the ratio of carbon fibers to resin. This can make the carbon fibers effectively strengthen the resin matrix. It can improve the material’s wear – resistance and fatigue – resistance, thus extending the service life of the brake pads.
3.4 performance retention
Select raw materials whose performance is not easily degraded during long – term use. For example, resins and fibers with good thermal stability and chemical stability can ensure the consistency of the friction material’s performance during use. Add some additives that can inhibit material aging and performance degradation, such as anti – aging agents and stabilizers. These can effectively maintain the performance of the friction material. These additives can form a stable structure inside the material. They can slow down the performance decline caused by long – term use and environmental factors.
An appropriate proportioning of raw materials can make the friction material maintain relatively stable performance during the wear process. For example, adjust the ratio of friction agents and friction – increasing agents. This can make the friction material maintain a similar friction coefficient in the initial and later stages of wear. It can avoid significant performance changes due to wear. Control the proportioning of additives. Make them evenly distributed in the material. This can better play their role in inhibiting performance degradation. For example, an appropriate amount and uniform distribution of anti – aging agents can effectively prevent the aging of the resin matrix. Thus, it can maintain the overall performance of the friction material.
3.5 high – temperature stability
Choose high – temperature – resistant materials, such as ceramic fibers and aramid fibers. These materials can still maintain good mechanical properties and structural stability at high temperatures. This can improve the high – temperature stability of the friction material. Use materials with good heat – conduction properties, such as metal powders (copper powder, iron powder, etc.). These can quickly dissipate the heat generated during the braking process. They can reduce the temperature of the friction material, thereby improving its high – temperature stability.
Increasing the proportion of high – temperature – resistant materials can significantly improve the high – temperature stability of the friction material. For example, increasing the content of ceramic fibers in the friction material can enhance the strength and hardness of the material at high temperatures. This prevents deformation and performance degradation caused by high temperatures.
Properly matching the proportion of heat – conducting materials with other materials can optimize the heat – conducting performance of the friction material. For instance, adding an appropriate amount of copper powder can increase the thermal conductivity of the material. However, if the copper powder content is too high, it may affect the friction performance and mechanical strength of the friction material.
3.6 thermal deformation
Raw materials like ceramic materials and some special alloys, with high melting points and low expansion coefficients, can effectively reduce thermal deformation. They don’t soften or expand easily at high temperatures, keeping the friction material’s shape and size stable.
Choosing resin and fiber materials with good thermal stability and low thermal decomposition susceptibility helps lower the risk of thermal fade. High – performance polyimide resin is a good example. It has good thermal stability, maintaining mechanical and friction properties at high temperatures and reducing thermal fade.
Optimizing raw material proportions is also crucial. Adjusting the ratio of ceramic particles to resin, for instance, can form a skeleton structure in the resin matrix. This improves the material’s high – temperature rigidity and reduces thermal deformation.
Finally, controlling the content of thermally decomposable materials is necessary. Reducing easily decomposable organic additives in the friction material can cut down on thermal fade and enhance braking performance stability.
3.7 mechanical strength
High – strength fiber materials, such as carbon fibers and aramid fibers, can significantly improve the tensile strength and tear – resistance of the friction material. These fibers can play a reinforcing role in the resin matrix. They can withstand the tensile and shear forces generated during braking.
Select a resin with good bonding properties as the matrix material. It can firmly bond the fibers and other fillers together, forming a whole. This can improve the overall mechanical strength of the material.
Increasing the content of fiber materials can enhance the mechanical strength of the friction material. However, when the fiber content exceeds a certain proportion, it may lead to poor material fluidity and difficult molding. This will instead affect the mechanical strength. For example, when the carbon fiber content is too high, the friction material is difficult to distribute evenly during the pressing process. It will have local defects and reduce the overall strength of the material.
Reasonably adjust the proportion of resin, fibers, and fillers. This can make the material reach the best mechanical strength. For example, optimize the amount of resin. Make it fully wrap the fibers and fillers without reducing the material’s rigidity due to excessive amount. This can improve the impact – resistance, compression – resistance, and shear – resistance of the friction material.
4. Common bicycle disc brake pads types: pros and cons
Based on the different friction materials used, common bicycle disc brake pads types can be divided into four categories: resin disc brakes, metal disc brakes, semi – metal disc brakes, and ceramic disc brakes. In the bicycle braking system, brake pads of different materials show distinct performance characteristics through their unique material formulas.
4.1 Resin friction material brake pads
The formula of resin brake pads is based on phenolic resin as the main binder. This polymer has excellent viscoelasticity at room temperature. It usually accounts for 20 – 40% of the formula. To enhance mechanical properties, 5 – 15% of glass fibers or aramid fibers are added. These fiber materials form a network – like support structure at the micro level. Friction modifiers such as graphite and rubber particles account for about 10 – 20%. They can optimize the surface friction characteristics and reduce noise. The remaining part consists of hard fillers such as silica and alumina. They are used to adjust the overall hardness and heat – dissipation performance.
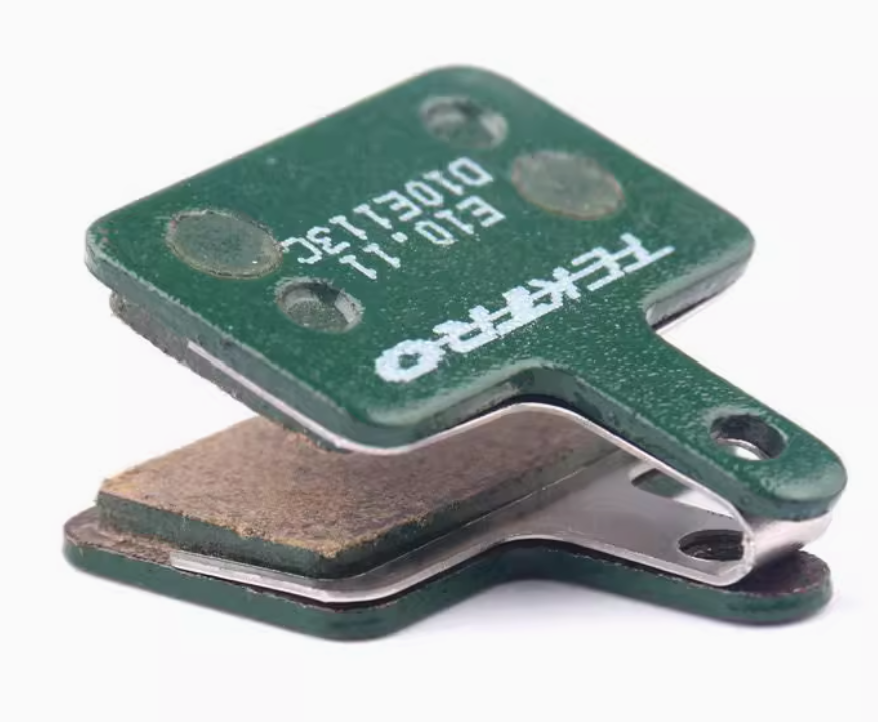
PROS &CONS
The advantage of this organic composite material is that it can provide a high friction coefficient of 0.4 – 0.6μ. The braking response is sensitive, and the noise is extremely low. It is especially suitable for urban riding and dry environments. However, the nature of its organic matrix also brings obvious limitations. When the temperature exceeds 200°C due to continuous braking, the phenolic resin will undergo thermal decomposition and carbonization. Not only will the friction coefficient drop sharply, but an uneven carbonized layer will also form on the material surface. This is a typical thermal fade phenomenon. The low softening temperature of the resin also leads to a relatively fast wear rate. The service life is usually only 500 – 1000 kilometers. In addition, the porous organic matrix is easy to absorb moisture. It will cause braking force fluctuations in a humid environment.
4.2 Disc brake pads made of metallic friction materials
Metal brake pads adopt a completely different material system. Their core consists of 50-70% metal powder (mainly copper, iron and their alloys), which forms a porous yet sturdy metal matrix through a high-temperature sintering process. During this sintering process, a metallurgical bond is formed between the metal particles, endowing the material with extremely high mechanical strength. To improve the friction characteristics, 5-15% of graphite or molybdenum disulfide is added as a solid lubricant. They can form a transfer film at the friction interface, reducing noise and controlling wear. Hard particles such as 10-20% of silicon carbide or zirconia serve as friction enhancers to ensure sufficient braking force.
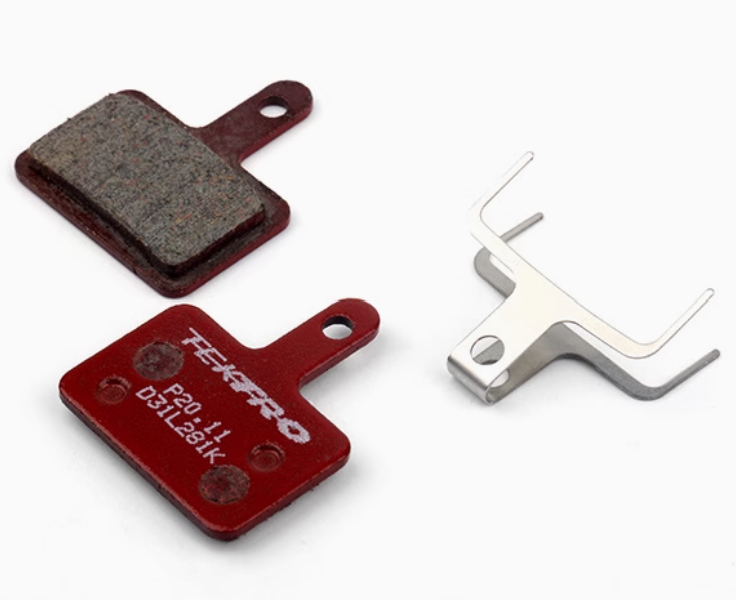
PROS &CONS
The greatest advantage of the metal formulation lies in its excellent high-temperature stability. Due to the fact that the melting point of copper is as high as 1083℃ and that of iron reaches 1538℃, there will be no thermal fade under normal braking conditions. Its friction coefficient remains between 0.3-0.5μ. Although its performance is mediocre when cold, it will become stable as the temperature rises, making it especially suitable for harsh working conditions such as long downhill rides. The high wear resistance of the metal matrix enables its service life to reach over 2000 kilometers.
However, the direct contact between the metal and the disc will generate relatively high noise, and it will take a longer time to reach the optimal operating temperature in low-temperature or humid environments. From a microscopic perspective, although the porous structure of the metal sintered body is beneficial for heat dissipation, it may also accumulate pollutants and affect performance.
4.3 Disc brake pads made of semi-metallic friction materials
Semi-metallic brake pads aim to find a balance between two extremes. Their typical formulation includes 30-50% metal powder, 20-30% modified resin, and 10-15% ceramic or steel fibers. This composite design keeps the friction coefficient within an ideal range of 0.4-0.55μ, retaining some heat resistance of the metal material while improving the low-temperature performance through the resin component.
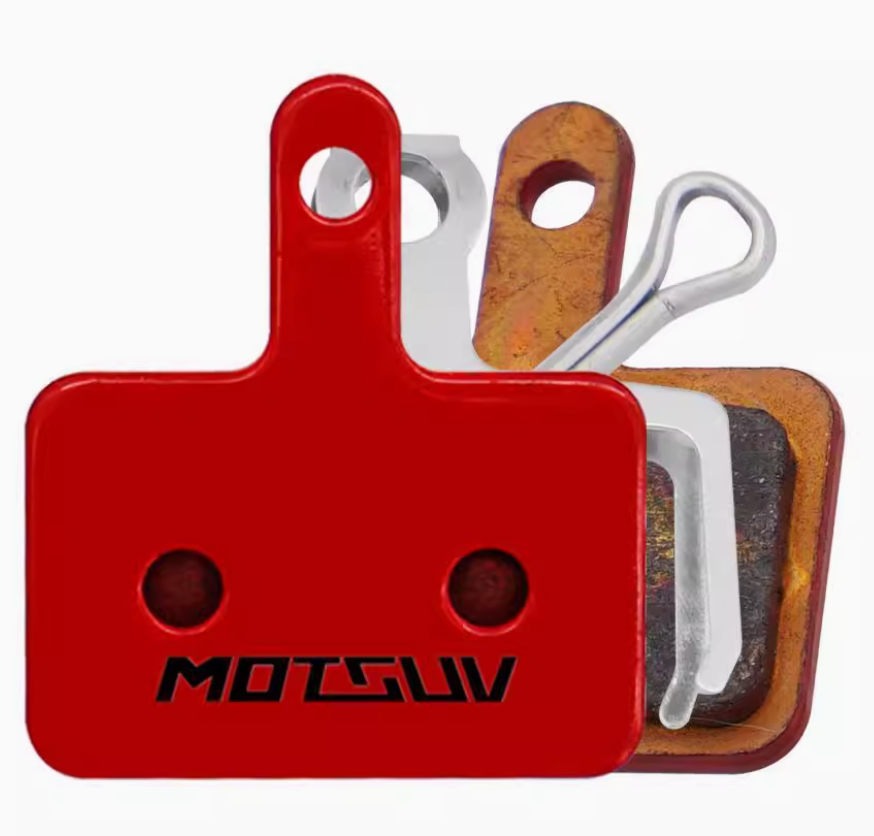
PROS &CONS
In practical use, its performance is indeed more balanced: at high temperatures, the metal components can maintain the basic braking force, and the resin ensures the initial response. The service life is about 1000-1500 kilometers, which is between that of pure resin and pure metal. However, this compromise also means concessions. When the temperature exceeds the tolerance limit of the resin, although the metal skeleton can still provide braking force, the overall performance will significantly decline. In addition, the presence of resin still brings the problem of water absorption, but the degree is less than that of the pure resin formulation.
4.4 Disc brake pads made of ceramic friction materials
Ceramic brake pads represent the most advanced braking material technology. Their formulation typically contains 30-50% silicon carbide or aluminum oxide ceramic fibers, and these materials have a Mohs hardness of over 9 and a melting point of more than 2000℃. To improve thermal conductivity, 20-30% copper or nickel powder is added. The binder system may be modified resin or more advanced ceramic adhesive, accounting for about 10-20%. The remaining part consists of lubricating components such as graphite. This formulation results in nearly perfect braking performance: the friction coefficient is stable at 0.45-0.6μ, there is no thermal fade problem at all, and the service life easily exceeds 3000 kilometers.
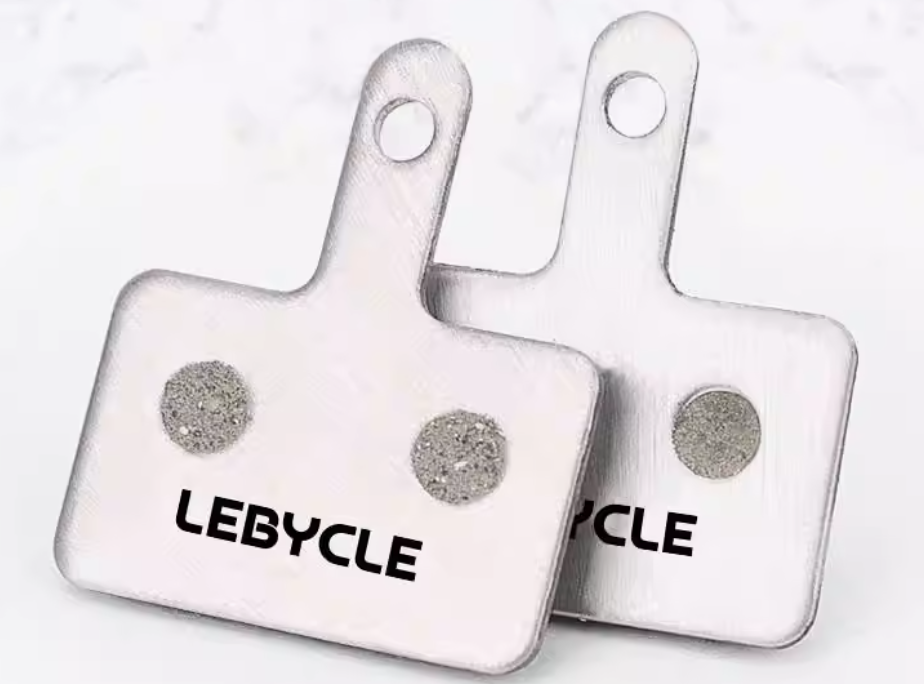
PROS &CONS
The intrinsic properties of ceramic materials make them almost unaffected by environmental humidity, and the braking process is extremely quiet. From the perspective of materials science, ceramic fibers form a nanoscale self-lubricating transfer film during the friction process, which ensures the braking force while reducing wear. However, the cost of achieving these advantages is extremely high. Ceramic powders require precise particle size control and complex sintering processes, and the use of precious metals in the formulation further increases the price. In addition, ceramic materials have insufficient surface roughness at extremely low temperatures, and a short running-in period is required to reach the best state.
The deep-seated reasons for these performance differences can all be explained in materials science. In practical applications, formulation engineers seek the optimal balance among the friction coefficient, wear resistance, noise control, and cost by carefully regulating the proportion, particle size, and distribution of each component. With the development of nanotechnology and composite materials science, new mixed formulations are breaking through the performance boundaries of traditional materials, bringing safer and more durable solutions to bicycle braking systems.
5 How to choose among different materials for your bicycle?
5.1 Riding environment and climate conditions
5.1.1 Mountain biking on harsh road conditio
Among all bicycle disc brake pads types, if you often engage in long-distance downhill rides, off-road cycling, or high-intensity cycling, it is preferable to choose metal brake pads (fully sintered metal). Their high-temperature resistance can effectively resist thermal fade, and they can maintain stable braking force even in environments with heavy mud and sand contamination. The wear resistance of the metal material can also withstand the wear caused by frequent braking.
Note: It is necessary to pair them with metal brake discs (such as stainless steel discs); otherwise, it may accelerate the wear of resin brake discs.
5.1.2 Road Cycling / Dry Urban Roads
Among all bicycle disc brake pads types, resin brake pads are recommended here. Their high initial friction coefficient (0.4-0.6μ) can provide a sensitive braking response, which is suitable for urban cycling that requires frequent tapping of the brakes. The silent characteristic has a significant advantage on flat roads, but long continuous braking should be avoided to prevent thermal fade.
5.1.3 Rainy/Wet Environment
Among all bicycle disc brake pads types, maybe you should choose ceramic brake pads or metal brake pads here. The inert nature of ceramic materials makes them completely waterproof, and there will be no fluctuations in braking force due to humidity. Although the porous structure of metal brake pads may accumulate water, the water can evaporate quickly at high temperatures, and their overall performance is better than that of resin brake pads. Avoid resin brake pads: The friction coefficient may decrease by 20-30% after they absorb water.
5.1.4 Mixed Road Conditions/Commuting
Among those bicycle disc brake pads types, semi-metallic brake pads are an ideal choice here. Their balanced design takes into account the low-temperature sensitivity of resin and the high-temperature resistance of metal, making them suitable for scenarios where occasional steep slopes need to be dealt with but flat roads are the main part of the journey.
5.2 Riding Demands
5.2.1 Extreme Braking Force
Among all bicycle disc brake pads types, ceramic brake pads can provide the highest and most stable friction coefficient (0.45 – 0.6μ) in dry environments, which is suitable for competitive-level requirements. However, attention should be paid to their low-temperature running-in characteristics – the initial braking may be slightly weaker in cold weather.
5.2.2 Long Service Life/Low Maintenance Cost
The service life of metal or ceramic brake pads far exceeds that of resin ones. For example, metal brake pads can last more than 2000 kilometers under normal use, and ceramic brake pads can even last more than 3000 kilometers, which is suitable for users who don’t want to replace parts frequently.
5.2.3 Quiet Operation
Resin and ceramic brake pads generate the least noise, which is especially suitable for night riding or community commuting. Metal brake pads may produce sharp noise in wet environments, and this can be alleviated by adding noise reduction pads or choosing formulations with a higher proportion of graphite.
5.2.4 Lightweight
Resin brake pads are the lightest (about 20 – 30g per pair), followed by semi-metallic ones (30 – 40g), and metal and ceramic brake pads are the heaviest (40 – 60g). Road cyclists who are sensitive to weight can preferentially choose resin or semi-metallic brake pads.
5.3 Special Scenarios
5.3.1 Winter/Extremely Cold Environments:
Among all bicycle disc brake pads types, metal brake pads are preferred here. Their low-temperature preheating characteristics (quick heat generation through friction) enable them to enter the working state more quickly. Ceramic brake pads may require a longer running-in period when the temperature is below -10°C.
5.3.2 Loaded Riding/Touring Bikes:
Metal or ceramic brake pads have higher mechanical strength and can withstand the continuous braking pressure of heavier loads.
5.3.3 Electric Assist Bicycles (E-Bikes):
Due to higher speeds and heavier vehicle weights, metal or ceramic brake pads must be chosen. Resin materials cannot meet the requirements of high-frequency braking.
By the way, SUMLON has been manufacturing bicycle parts for over 15 years. Contact us if you are looking for a bike parts factory or a one-stop wholesaler. Peace